With 20 years'development, Haomei has grown into a top aluminium alloy manufacturers and suppliers. We have comprehensive kinds of aluminium sheets, aluminum coil, aluminum strip, aluminum foil, aluminum discs, aluminum tread plate, color coated aluminum and CTP plates, covering series-1, series-3,series-5, series-6 and series-8. You can realize one-stop purchase in Haomei.
How Is White Aluminum Coil Stock Produced
Aluminum Strip for Transformer Winding
Transformer aluminum strip is a commonly used conductive material in power transformers, which plays an important role in power transmission and distribution. In order to ensure that the transformer can operate normally and have good electrical conductivity, standards have been established for the thickness and width of the transformer aluminum strip.
Thickness standard of transformer aluminum strip
The thickness standard of transformer aluminum strip plays an important role in ensuring the electrical conductivity and mechanical strength of the transformer. According to international standards, the thickness of transformer aluminum strips should meet the following requirements:
1. Standardized thickness: According to the power and current load of the transformer, as well as the requirements of the use environment, the thickness of the transformer aluminum strip should comply with the corresponding international standards. Normally, the thickness standards of transformer aluminum strips are generally 0.2mm, 0.3mm, 0.4mm, etc.
2. Thickness tolerance: In order to ensure the accuracy of the production and use of transformer aluminum strips, thickness tolerance is an important indicator. Generally speaking, international standards stipulate that the thickness tolerance of transformer aluminum strip is ±0.02mm to ensure its accuracy during production and use.
Width standard of aluminum strip for transformer
The width standard of the transformer aluminum strip is a key factor in ensuring the conductive performance and safe operation of the transformer. The following are key points regarding transformer aluminum strip width standards:
1. Standardized width: The width of the transformer aluminum strip should comply with the corresponding international standards. According to the power and current load of the transformer, as well as the design requirements, the width standards of transformer aluminum strips are generally 30mm, 50mm, 80mm, etc.
2. Width tolerance: In order to ensure the accuracy of production and use of transformer aluminum strips, width tolerance is an important consideration. Generally, international standards stipulate that the width tolerance of transformer aluminum strips is ±0.5mm to ensure accuracy during production and use.
The thickness and width standards of aluminum strips for transformer winding are formulated to ensure the normal operation and safe use of transformers. When selecting aluminum strips for transformers, we should choose a thickness and width that meet the standards based on actual needs. At the same time, during production and use, we should also strictly control the thickness and width tolerances of the transformer aluminum strip to ensure its accuracy and stability. Haomei Aluminum also provides aluminium foil for transformer winding.
During the production, use and maintenance of transformer aluminum strips, we also need to pay attention to the following points:
1. The thickness and width of the transformer aluminum strip should be checked regularly to ensure that it meets the standard requirements. If there is any abnormality, repair or replace it in time.
2. Pay attention to the storage and handling of transformer aluminum strips to avoid moisture and damage. During the transportation process, corresponding protective measures should be taken to ensure the integrity of the transformer aluminum strip.
3. It is necessary to strengthen the protection and maintenance of the transformer aluminum strip, regularly clean and apply protective coating to extend its service life.
In addition to the thin aluminum strips, we also have rich specifications of aluminium strips like aluminium strip 2mm. Welcome to leave message below to inquire what you need.
Original source: https://www.aluminumstrip24.com/news/aluminum-strip-for-transformer-winding.html
2xxx Aluminum Alloys: 2024 Aluminum Sheet
2xxx aluminum alloys belong to the Al-Cu-Mg alloy, which is called high-strength hard aluminum and is the most widely used structural aluminum alloy. The tensile strength of 2xx series aluminum alloy is 400~500 MPa, which is lower than the room temperature strength of 7xxx series aluminum alloy, but its heat resistance, fatigue characteristics, especially fatigue crack propagation resistance are better than those of 7xxx series aluminum alloy.
2000 series aluminum alloys have higher strength, and the alloy strength of 2xxx grades can compete with steel. However, due to differences in copper content, the strength and corrosion resistance of this series vary within a wide range to meet different needs.
Among them, the corrosion resistance of alloys with lower copper content is close to that of rust-proof aluminum; the strength of alloys with higher copper content is close to that of hard aluminum, which is actually equivalent to increasing the silicon content on the basis of hard aluminum.
Among the 2000 series aluminum alloys, the 2024 alloy invented in 1939 is the more commonly used one. 2024 alloy has brought huge changes to the structure and performance of aircraft, and also laid the foundation for the development of 2000 aluminum alloys.
2024 has a density of 2.78 g/cm 3 (0.1 lb/in 3 ), a conductivity of 30% IACS, and a Young's modulus of 73 GPa (10.6 Msi) in all states at 500 °C (932 °F). The composition of 2024 aluminum alloy roughly includes 4.3-4.5% copper, 0.5-0.6% manganese, 1.3-1.5% magnesium and less than 0.5% silicon, zinc, nickel, chromium, lead and bismuth.
2024 aluminum sheet has high strength and certain heat resistance, and can be used as working parts below 150℃. At temperatures above 125°C, the strength of 2024 alloy is higher than that of 7075 aluminum plate. The formability is relatively good in the hot state, annealed and newly quenched states, and the heat treatment strengthening effect is significant, but the heat treatment process requirements are strict.
The common tempers of 2024 aluminum is T3, T351 and T4. 2024 t351 aluminum has high plasticity, fatigue life, fracture toughness and resistance to fatigue crack growth, but poor corrosion resistance. This alloy thick plate is mainly used in fuselages, wings, shear floors and webs, and other structural parts with high strength requirements.
Original site: https://www.aircraft-aluminium-sheet.com/a/2xxx-aluminum-alloys-2024-aluminum-sheet.html
5182 and 6101 Aluminum Alloys for Automobile
With the rise of new energy vehicles and the development of the energy Internet, busbars will replace standard cables and are widely used in the manufacturing of new energy vehicles, as well as in emerging industries such as robot manufacturing, smart grids, and photovoltaic equipment. In particular, soft busbars have become an important power transmission technology in the new energy field.
Soft busbar has the advantages of high transmission efficiency, safety and stability, and small footprint, so it is widely used in charging piles, power distribution cabinets, power replacement equipment and other fields.
6101 aluminum alloy has medium strength and high electrical conductivity and can be used for long-distance power transmission lines. Compared with traditional steel-core aluminum alloy stranded wire (ACSR), all-aluminum alloy stranded wire (AAAC) twisted from a single Al-Mg-Si alloy wire can well avoid electrical corrosion and can improve power transmission efficiency.
At the same time, the maintenance cost of transmission lines is reduced. More importantly, the Al-Mg-Si series alloys are heat-treatable strengthened alloys, and their strength and conductivity can be adjusted by solid solution + aging heat treatment.
ABS car panels have high requirements on the mechanical properties of aluminum plates, and have strict standards for the flanging performance and surface quality of the aluminum plates. The cold rolling rate of BS is generally required to reach 85%. Conventional aluminum alloys used for ABS include: 2002, 2117, 2036, 2037, 2038, 3004, 5052, 5182, 6009, 6010, 6015, 6016, 6111, etc. Except for 3004 and 5182 aluminum alloys which are used in the O state and 5052 alloy which are used in the H32 and H34 states, other alloys are used in the T4 state.
In terms of deep stamping performance and tensile strength, 5052 aluminum alloy is far less good than 5182 alloy. Therefore, the first choice aluminum alloy for inner panels of complex shapes is 5182-O aluminum sheet. Find 5182 o aluminum properties from Haomei Aluminum.
The car doors, hood panel and trunk lid all can choose 5182 aluminum alloy. Since the 5182 aluminum plate has excellent deformability, it can absorb the impact very well when it is hit by external forces, protecting the driver and passengers to a great extent.
The mainstream automobile aluminum sheet production technology: semi-continuous casting (direct chill casting, DC) to produce large- sized flat ingots- sawing the head and tail- cutting the surface- heating- high-temperature rolling in a large wide-width hot rolling unit- aluminum coil- cold rolling process to finished product thickness- heat treatment with air cushion continuous heat treatment furnace. If it is necessary to control the material microstructure and grain size, an intermediate annealing process can be added to the cold rolling pass.
Haomei Aluminum has main 5xxx and 6xxx aluminum alloys. Welcome to leave message below to inquire what you need.
Original site: https://www.aluminium-auto-sheet.com/a/5182-and-6101-aluminum-alloys-for-automobile.html
The Use of 1561 Aluminum in Shipbuilding
As ship manufacturing develops in the direction of lightweight, high-speed, and large-scale, aluminum-magnesium alloys with small density, high specific strength, and good stability have become the preferred materials to replace marine steel. In the past, 5083 aluminum alloy was mostly used in shipbuilding, but the orthopedic treatment after welding had a greater impact on the manufacturing accuracy.
1561 aluminum alloy (Russian brand) has higher strength than 5083 aluminum alloy. Using 1561 aluminum alloy as marine material will improve the quality and performance of ships. 5059 and 1561 aluminum alloys are the most high-end marine aluminum alloys and are currently recognized as the most technically difficult high-end marine aluminum alloys in the industry.
1561 aluminum alloy is a new anti-rust aluminum alloy developed based on the existing Al-Mg series marine aluminum alloy to increase the Mg and Mn content and reduce the impurity element content to meet the needs of high corrosion-resistant load-bearing components.
1561 aluminum alloy has high yield strength and small elastic modulus. It has a large rebound after multi-point forming. Small deformation can basically fully rebound after unloading. Therefore, 1561 aluminum alloy needs to be given a larger amount of springback compensation during the forming process.
When the curvature of the formed part is large, the 1561 aluminum alloy is prone to wrinkles during one-time forming. However, after adopting the multi-pass forming method, the problem of wrinkling in the center of the formed part is solved, and the forming error ± 1 mm area is increased by 80% to to 91%. The error is reduced and the forming accuracy is improved.
1561 aluminum alloy is an aluminum alloy with a high magnesium content. It is very easy to produce defects such as pores and cracks during the welding process. How to ensure that these defects do not occur in the welds during the hull construction process is a key issue to ensure production quality. The TIG deep penetration welding process is used to weld 1561 high magnesium aluminum alloy, which can significantly reduce defects such as pores and inclusions in the weld.
As one of the big marine grade aluminum plate suppliers in China, Haomei Aluminum can provide you 5052, 5083. 5086, 5059, 1561 aluminum sheets. Welcome to leave message below to inquire what you need.
Orignal site:https://www.marine-aluminium-plate.com/a/the-use-of-1561-aluminum-in-shipbuilding.html
Aluminum Plate for Special Vehicles
Aluminum alloy, with its unique advantages of low density, corrosion resistance, energy saving and environmental protection, is gradually used in large quantities in special vehicles and has become the main material for lightweight.
Tanker Truck
Compared with ordinary carbon steel and stainless steel tank trucks, aluminum alloy tank trucks can not only significantly reduce the weight of the vehicle, improve transportation efficiency, but also extend the service life of the tank.
Its corrosion resistance is more than 70% higher than that of traditional carbon steel. This feature greatly reduces the maintenance costs related to the tank. The internal cleanliness of the tank is high, and it has good energy saving and environmental protection effects.
Aluminum alloy 5083, 5454 and 5182 are currently commonly used tanker aluminum sheets. They can be used to make tanker body, baffle and tanker head. The aluminum alloy tank truck can load oil, gasoline, chemicals, cement and other dense materials.
Vans
Aluminum alloy vans mainly include aluminum alloy van semi-trailers and aluminum alloy wing opening transport vehicles. According to the usage rate of aluminum alloy in the vehicle, it can be divided into all-aluminum alloy vans and steel-aluminum hybrid vans.
An all-aluminum alloy van means that the frame and body are made of aluminum alloy; a steel-aluminum hybrid van means that part of the vehicle structure is made of aluminum alloy, such as the carriage body is made of aluminum alloy while the frame is still made of steel. The aluminum alloys available for van trucks are aluminum plates, aluminum alloy profiles, aluminum honeycomb panels, aluminum castings, etc. Due to the advantages of high strength and easy molding of aluminum alloy profiles, aluminum alloy profiles are preferred for manufacturing.
Aluminum alloy vans have long been popular in European and American markets. Because of its light weight, large loading space, beautiful appearance, and the ability to print advertisements on the surface, it occupies a leading position in the US market. The alloys used in aluminum alloy profiles for containers mainly include 6061, 6082, 6351, 6005, 6063 and 6060, among which 6061 and 6082 alloys account for more than 90%. Asia and the United States mainly use 6061 alloy, while European vans mainly use 6082 alloy.
Refrigerated trucks
Refrigerated trucks are closed van transport vehicles used to transport frozen or fresh-keeping goods, including bread-type refrigerated trucks, van-type refrigerated trucks and semi-trailer refrigerated trucks. The biggest difference in the relationship between properties and temperature between aluminum and steel is that steel has low-temperature brittleness, while aluminum and aluminum alloys do not. When the temperature decreases, while the strength and performance of aluminum and aluminum alloys increase, the plasticity also increases as the temperature decreases. Therefore, aluminum alloys become good materials for low-temperature equipment.
Haomei Aluminum provides 5083, 5754, 5454, 5059 and 5182 aluminum alloy for special vehicles, especially fuel tankers, semi trucks, LNG tank,etc. Welcome to leave message below to inquire what you want.
Original site: https://www.aluminium-tanker-plate.com/a/aluminum-plate-for-special-vehicles.html
Aluminum Alloy Fuel Tanker VS Other Fuel Tank Truck
Oil tank trucks are divided into refueling trucks and oil transport trucks. Whether they are refueling trucks or oil transport trucks, they are composed of a hazardous chemicals chassis, a top tank and an auxiliary system.
The difference between a refueling truck and an oil transport truck is that the refueling truck is equipped with a refueling machine, while the oil transport truck does not have a refueling machine. The raw materials of the fuel tanker are generally ordinary carbon steel, aluminum alloy, and stainless steel. After investigation, it was found that among these three materials, aluminum alloy tank trucks have the highest sales volume. Why is this?
The same car model can pull more if it uses an aluminum alloy tank body. The tank body of an aluminum alloy tank truck is made of aluminum-magnesium alloy like 5083 aluminum plate or 5754 h111 aluminum. The density of the material is relatively small, so a tank with the same volume is lighter than carbon steel. For example, a 28-square-meter aluminum alloy oil tanker is 2 tons lighter than a carbon steel tank.
Generally, the total weight of the same type of tank truck is the same, so the lighter the curb weight, the heavier the rated load, and the more fuel that can be loaded. It will bring more profit return quickly.
Oil tank trucks use aluminum alloy tanks, which are not easy to rust and do not pollute the oil. Aluminum reacts chemically with oxygen to produce aluminum oxide, which is aluminum rust. Aluminum rust is very thin, with a thickness of only one ten thousandth of a millimeter. But it is very hard and very wear-resistant. It adheres closely to the surface of the aluminum, preventing the aluminum inside from contacting the outside air and preventing the aluminum from continuing to rust. Therefore, the aluminum alloy tank will not pollute the oil during transportation. There are also no impurities produced during the process.
Aluminum alloy tank trucks have a lower relative center of gravity because of their lighter tanks, making them safer and more fuel-efficient. The weight of carbon steel is almost three times that of aluminum alloy tanks with the same volume.
Stainless steel tanks are as corrosion-resistant as aluminum alloy tanks, but aluminum alloy tanks are cheaper than stainless steel tanks. The recycling value of aluminum alloy tanks is much higher than carbon steel tanks. This is why most people choose aluminum alloy fuel tankers. Welcome to contact us for learning more about 5754 and 5083-h116 aluminum properties.
Original Source:https://www.aluminumtankerplate.com/a/aluminum-alloy-fuel-tanker-vs-other-fuel-tank-truck.html
What Are Aluminum Trim Coil Colors
The color coated aluminum coil refers to a material that is surface-coated to form a variety of colors to improve the oxidation protection performance and aesthetics of the aluminum coil. In daily life, color-coated aluminum coils are widely used in construction, decoration, automobiles, electrical appliances, packaging and other fields, and have become an important part of many products.
It has the advantages of both aluminum sheets and organic materials. The aluminum trim coil has the mechanical strength, good toughness, and easy processing and molding of aluminum sheets, but also have the good coloring, decoration, and corrosion resistance of organic polymer coating materials. It is easy to perform punching, bending, deep drawing, welding and other processing.
Because there are many aluminum trim coil colors, Haomei Aluminum generally does not have them in stock. The colors can be customized according to the RAL color card or other standard color card numbers, or they can be color-matched and processed according to samples, so color-coated aluminum coils require a certain period of time. Users should consider the processing time when ordering, and try to order in advance to avoid being late for processing.
The processing cycle of fluorocarbon color-coated aluminum coils is generally longer, mainly because the fluorocarbon paint uses Nippon Paint, and Nippon Paint's paint blending is all standardized. Color mixing will be carried out after the laboratory data is stable, so the delivery time of the PVDF coated aluminum coil is around 15 days. If we have aluminium coil in stock, the delivery time can be shortened to around 7 days.
The processing cycle of polyester color-coated aluminum coils is slightly shorter, because the color mixing of polyester paint is relatively simple. Generally, the processing cycle of the PE coated aluminum coils is about 2 days faster, mainly because the color mixing time is shorter.
Applications of painted aluminum coils
In terms of construction, the pre painted aluminium coil can be made into building exterior wall insulation materials, profiled panels, roof panels, ceilings, etc. It can provide a wide range of color choices and textures, and can also enhance the waterproof, anti-oxidation, and fire-proof capabilities of building exterior walls and roofs. They also have excellent sound absorption and decorative properties, making them beautiful and practical.
In terms of automobiles, color-coated aluminum coils can be made into automobile exterior decorative parts, such as doors, hoods, etc. Color-coated aluminum coils are lightweight, wear-resistant and low-cost, so they are widely used in the automotive industry.
In terms of electrical appliances, color-coated aluminum coils can be made into the casings of refrigerators, washing machines, air conditioners and other home appliances. Color-coated aluminum coils have a beautiful appearance and will not fade or change color. They can improve the grade and texture of home appliances and make home life better.
In terms of packaging, coated aluminum coils can be made into various forms of food, cosmetics and other packaging boxes to improve the quality and grade of the product. Welcome to leave message below to tell what you need.
Original source: https://www.hm-alu.com/a/what-are-aluminum-trim-coil-colors.html
What Are Properties and Uses of Aluminium 7000 Series
The yield strength of aluminum 7000 series is usually between 300-500MPa, which can effectively resist deformation caused by external loads. The alloy has good heat treatment properties and corrosion resistance. Heat treatment can significantly increase its strength and hardness while improving its corrosion resistance.
7 series aluminum alloys are widely used in the manufacture of aircraft structural parts and other parts requiring high strength, such as engine parts, landing gear, seats, etc. In addition, 7 series aluminum alloy can also be used to manufacture other mechanical parts that require high strength, high hardness and wear resistance, such as gears, shaft parts, etc.
Matweb aluminum 7075 is one of its main grade. It can be used in the aerospace industry, blow molding (bottle) molds, ultrasonic plastic welding molds, golf ball heads, shoe molds, paper molds, foam molding molds, dewaxing molds, templates, fixtures, mechanical equipment, aluminum alloy bicycle frame.
7075 aluminum's medium and thick plates, extrusions, free forgings and die forgings are used for the aircraft structural parts. The requirements for alloys in manufacturing such parts are high resistance to spalling corrosion, stress corrosion cracking, fracture toughness and fatigue resistance.
Features of 7000 aircraft aluminum alloys
High strength: The strength of 7 series aluminum alloy is much better than that of mild steel. Its main alloying elements are zinc and magnesium. The MgZn2 structure formed by zinc and magnesium has obvious strengthening effect, making the heat treatment effect of 7 series aluminum plates far better than other aluminum plates. As the zinc and magnesium content increases, the strength of the aluminum plate will further increase. Especially when the temperature is lower than 150℃, the performance is better.
High mechanical properties: 7 series aluminum alloys have excellent mechanical properties, including high strength, hardness and good plasticity. Due to the small and even distribution of internal crystals, the 7 series aluminum plate has super wear resistance, and its high level of drilling performance is also rare. These properties make it suitable for manufacturing aircraft parts that need to withstand heavy loads and high-speed movements.
Strong corrosion resistance: 7 series aluminum alloy can resist corrosion and oxidation when exposed to the atmosphere. It has good resistance to stress corrosion and spalling corrosion, and performs well in the processing of high-stress structural parts. This makes it suitable for aircraft components in marine environments and other corrosive environments.
Easy to process: 7000 aluminum alloys can be processed into parts of various shapes and sizes through various processing methods such as casting, forging, extrusion and rolling, which can meet the strict requirements of aircraft manufacturing.
Lightweight: Because 7xxx aluminum alloy has high strength and hardness and relatively low density, it is suitable for manufacturing lightweight aircraft parts, helping to improve the fuel efficiency and performance of aircraft.
Good thermal conductivity: 7 series aluminum alloy has good thermal conductivity and can effectively transfer heat. It is suitable for manufacturing aircraft parts that need to withstand high temperatures and dissipate heat.
Disadvantages: Adding zinc and magnesium elements can improve the strength of 7 series aluminum plates. However, with the increase of zinc and magnesium elements, the resistance to stress corrosion and spalling corrosion of 7 series aluminum plates will also decrease. It should be noted that the 7 series aluminum alloy has a higher hardness and is more difficult to process, requiring fine machining and heat treatment operations.
Haomei Aluminum has different grades of 7000 aluminum alloys like matweb aluminum 7075 and 7050 aluminum alloy. Welcome to leave message below to inquire what you need.
Original Source:https://www.aircraftaluminium.com/a/what-are-properties-and-uses-of-aluminium-7000-series.html
Que es un ctp
La impresión offset es una técnica de impresión común en la que una imagen entintada se transfiere desde una plancha de impresión a una mantilla y luego a la superficie de impresión. Específicamente, la plancha de impresión debe poder transferir la imagen al papel u otro sustrato. Las planchas de impresión suelen estar hechas de láminas de impresión de aluminio. Existen principalmente dos tipos: ctp offset y plancha PS.
Para las aplicaciones planchas ctp, lo primero que nos viene a la mente son las empresas de impresión de periódicos. Sin embargo, a juzgar por el desarrollo de los últimos dos años, las empresas de impresión comercial, especialmente aquellas que buscan calidad de impresión, se han convertido en las protagonistas de las aplicaciones CTP.
En términos del proceso de impresión CTP, debido a que la información de diseño de la publicación se envía directamente a la plancha de impresión, en comparación con la impresión PS, el enlace de salida de la película y el enlace de impresión de la plancha PS se reducen, por lo que el costo del enlace de impresión CTP incluye: Tarifa de impresión de muestra digital de salida, tarifa de impresión (tarifa de fabricación de planchas CTP) y tarifa de impresión.
Las empresas de impresión comercial y de embalajes que tienen altos requisitos de calidad de impresión realizan principalmente tareas de impresión como álbumes de alta calidad y productos de embalaje exquisitos, y todas eligen la plancha CTP térmica. El CTP térmico se caracteriza por utilizar un láser con una longitud de onda de 830 nm o 1064 nm para grabar la plancha de impresión.
La tecnología Violet CTP utiliza planchas de impresión violetas de alta sensibilidad especialmente producidas para ella. El grano de las planchas de impresión violetas es más fino que el de las planchas tradicionales y el proceso de recubrimiento es más complejo. Por supuesto, la capa fotosensible también es diferente de las placas de PS tradicionales. Tras su desarrollo en los últimos años, se ha convertido en las tres principales tecnologías CTP junto con el CTP térmico y el CTCP.
El espesor de la lámina de aluminio para placas CTP es generalmente de 0,280 mm, que es ligeramente más grueso que el de las placas de PS producidas actualmente (el espesor de la base de la placa de PS es de 0,270 mm ± 0,005 mm). Algunas empresas extranjeras también utilizan una base de placa de aluminio de 0,275 mm de espesor y la tolerancia de espesor es de ±0,005 mm. Si la base de la placa de aluminio es más gruesa, la plancha de impresión a la venta será más rígida y será menos probable que se doble.
Haomei Aluminium no solo produce láminas de aluminio para impresión, sino que también suministra diferentes tipos de planchas offset como planchas PS, planchas CTP y planchas CTCP. Bienvenido a dejar un mensaje a continuación para solicitarnos planchas de impresión de aluminio.
sitio original: https://www.placadealuminio.es/a/que-es-un-ctp.html
3003 and 5052 Aluminum Alloy in Automobile Manufacturing
5000 series deformed aluminum alloy automobile sheets are mainly strengthened by solid solution strengthening and fine grain strengthening of magnesium atoms and a small amount of solid solution and precipitation strengthening of copper atoms. This series of alloys has good formability.
When left at room temperature, the yield point is prone to prolongation (or lüders elongation), and the surface is prone to wrinkles after stamping, which affects the appearance quality of the product. The increase of iron element will significantly worsen its ductility and cold bending performance; due to the lack of bake hardening, the paint will easily soften after baking, thus affecting the dent resistance of the parts.
6000 series automotive aluminum sheets use silicon and magnesium as the main alloying elements (copper is also added as an alloying element in the 6111 alloy). This type of alloy relies on the precipitation strengthening of silicon and magnesium during solid solution aging as the main strengthening method. It can be heat treated and strengthened.
This type of aluminum alloy sheet has good formability in the pre-processed state and no yield point elongation. It is suitable for automobile exterior panels, and has bake hardening properties. It has high flow stress after the paint is baked, and the parts have high dent resistance; however, aging will lead to a decrease in flanging ductility and deterioration in formability.
Currently, the most commonly used aluminum alloy plates for cars are AA6016, AA6022, AA6111, AA6005, AA6009 and AA6010, AA5182, AA5754, AA5052, etc. The Audi A8 car uses 6016 alloy plates as the body panel, the Acura NSX car uses 5052 as the interior panel and the 6000 series as the exterior panel. The Jaguar XJ220 car and the GM EV1 car both use 5754 as the body covering material.
After searching the existing technology, it was found that the aluminum alloy inner panels used in automobiles are mainly 5xxx series alloys, such as 5052, 5182 alloys, etc. In terms of deep drawing performance and tensile strength, 5052 aluminum alloy is far less good than 5182 alloy. 5052 aluminum thickness for cars is not too thick.
The batteries that provide driving power for electric vehicles are called power batteries, including traditional lead-acid batteries, nickel-metal hydride batteries, and emerging lithium-ion power batteries. Currently, the world is promoting lightweight vehicles, and aluminum is a better choice. 3003 aluminum sheet is used for this aspect.
3003 h14 aluminum sheet has good formability and is mainly used as deep drawing materials. Using 3003 aluminum alloy products to make stamped parts, models, shells, etc. has many advantages such as good surface, good plasticity, and pressure resistance.
Original Source:https://www.autoaluminumsheet.com/a/3003-and-5052-aluminum-alloy-in-automobile-manufacturing.html
3003 Aluminum Foil for Food Container
3003 aluminum foil belongs to the aluminum-manganese alloy, Its strength is higher than that of 1 series aluminum foil, and is about 10% higher than 1100 aluminum foil and 1060 aluminum foil. 3003 aluminum foil is generally used in aluminum foil food container, food packaging, aluminum honeycomb cores, etc., and is deeply favored by the market.
The physical properties of food-grade aluminum foil include thickness, strength, elongation and surface smoothness. The chemical composition of food-grade aluminum foil is also one of the important contents of inspection. The food contact safety of food-grade aluminum foil is also a key part of inspection. 3003 aluminum foil make different types of food containers.
Baking aluminum foil boxes: They are mainly small-capacity boxes, basically less than 300ML. The most widely used is the 50ml baking aluminum foil box, which can be used for sauces, bowls, baked goods, desserts, puddings and other foods. Among them, there are also jam aluminum foil boxes of about 15-25g, which are also widely used.
Round food container: The large-capacity round aluminum foil container is mainly suitable for holding staple food, stew soup, and used as dry pot, hot pot, etc., such as whole chicken, whole duck, large portions of lobster, boiled fish, hot pot stew, Medium-capacity round aluminum foil container is suitable for holding fast food, fruits, soups, etc. Because the portion is suitable, it is similar to the portion required for a family's daily diet, and the overall demand is relatively high; then small-sized round aluminum foil boxes are more suitable for holding some small bowls of dishes.
Square aluminum foil container: It is mainly suitable for takeout packaging. Ordinary square aluminum foil boxes are suitable for holding fast food, fruits, rice, prepared dishes, etc.; the weight is similar to that required for daily meals at home, and it is an aluminum foil box with high demand. The large-capacity square aluminum foil box is mainly used for grilled fish trays. It is very suitable for takeout packaging of grilled fish.
Compared with ordinary packaging boxes, the outstanding advantage of aluminum foil container is that it maintains the taste of meals as freshly out of the pot to the greatest extent. The richness of the styles of aluminum foil containers determines the breadth of its application scenarios. The powerful functions and aesthetic appearance can also enrich our food life and improve the quality of catering services. Haomei Aluminum has rich aluminum foil types. Welcome to leave messae below to inquire what you need.
What Is Used For Making Aluminum Seal Cap
Aluminum seal caps come in a variety of styles and widths. It offers stability and stiffness compared to other materials. Aluminum caps and closures are frequently used in the food and beverage industry. The aluminum lid has a sturdy construction and is easy to open.
Aluminum caps and closures are made to suit the dimensions of bottles, containers and jar mouths. The aluminum bottle cap material is aluminum alloy sheet like plain or color printed aluminum sheet. Aluminum covers of different specifications need to be produced with aluminum alloy plates of different specifications.
Advantages of aluminum bottle caps
1. The aluminum cap is hygienic, will not rust, and is easy to open without the need for auxiliary tools. After opening, the bottle cap is destructive and can effectively prevent theft.
2. The aluminum cap has the advantages of good cushioning, shock resistance, heat insulation, moisture resistance, chemical corrosion resistance, etc. It is non-toxic, non-absorbent, does not cause dust or peeling, and has very good sealing performance.
3. The aluminum cap is resistant to high temperatures, boiling, alcohol, etc. The pattern design can use color printing, embossed characters, and milled characters.
4. The aluminum cap has excellent sealing properties and a larger flat surface on the cap surface, making printing of various text logos more beautiful.
Two types of aluminum bottle caps
PP caps: It refers to pilfer proof caps that are made of printed aluminum plates and liners and are sealed with a threaded bottle mouth and cannot be restored after opening and use. It is commonly used for sealing wine, soft drinks, health products, condiments, etc.
ROPP caps: It is short for Roll-on Pilfer Proof. When the closure is installed on the bottle, the threads are formed by applying a pressure roller to the closure. ROPP caps are in great demand in the beverage and food industries and are widely used in alcohol, medical, pharmaceutical, beverage, food, agrochemicals, edible oils, lubricants,etc.
Food- grade paint
Haomei Aluminum offers plain, coated and printed aluminum foil sheet for making various bottle caps. The coating and paint is of food grade. Food-grade paint is an environmentally friendly and safe paint product that is widely used in food, catering, medical, children's products and other fields that require contact with food or have high human safety requirements.
First of all, food-grade environmentally friendly paints strictly follow relevant laws, regulations and standards in terms of ingredients. They usually use harmless, low-volatile organic solvents and do not contain harmful substances such as formaldehyde, heavy metals, benzene, etc. It has passed a number of quality and safety certifications, such as European REACH regulations, US FDA certification, Chinese GB 4806.1 standards, etc., ensuring its safety for human health.
Secondly, food-grade paint causes less environmental pollution during the construction process. Due to its use of low-volatility solvents, it can reduce the emission of harmful gases, reduce the risk of air pollution, cause less pollution to the construction site and the surrounding environment, and is conducive to the protection of indoor air quality.
In addition, food-grade paint has good durability and adhesion to the painted items after use. It can effectively protect the surface of the coated items, prevent damage caused by moisture, stains, etc., and extend its service life.
It also performs well in terms of painting effects, providing a wide range of color choices and gloss to meet different painting needs. The white painted aluminium sheet is a popular choice. At the same time, it also has good water resistance, oil resistance, wear resistance and other properties, allowing the painted items to maintain a good appearance during long-term use.
Finally, food-grade paints are widely used in food, catering and other food-contact fields. For example, in food packaging, food processing equipment, restaurant kitchens, food display cabinets and other occasions, the use of food-grade paint can ensure that painted items will not contaminate food and ensure food safety.
Original Source: https://www.alclosuresheet.com/a/what-is-used-for-making-aluminum-seal-cap.html
What Are The Corrosion Resistance of Aluminum Alloy Grades
Aluminum corrosion is the gradual decay of aluminum molecules into their oxides, thereby reducing their physical and chemical properties. Aluminum is essentially a reactive metal, but it is also a passive metal. This means that while the nascent aluminum reacts with oxygen and water in the environment, the resulting compounds form a layer on the surface that protects the underlying material from further corrosion.
This non-reactive oxide layer adheres well to the surface and resists peeling, similar to stainless steel. Unlike deliberate processes such as laser etching, aluminum anodizing or brightening, corrosion is a slow process that can take place over months or years. Aluminum is unique in that there are many different types of corrosion pathways. Understanding these different corrosion phenomena is the basis for implementing control measures to reduce or completely prevent their occurrence.
The corrosion of aluminum and aluminum alloys mainly includes pitting corrosion, intergranular corrosion, stress corrosion cracking, lamellar corrosion, etc. The 6000 series alloy is the most popular among deformed aluminum alloys. Although its corrosion resistance is not as good as that of the 1000 series, 3000 series, and 5000 series aluminum alloys, it is much higher than that of the 2000 series and 7000 series aluminum alloys. 5000 series aluminum are the well known marine aluminum alloys.
The 6000 series alloy also has a relatively large intergranular tendency. The 6000 series aluminum alloy materials like 6082t6 grade aluminium used in important structures should be evaluated for intergranular corrosion sensitivity.
Judging from the corrosion morphology, the corrosion of aluminum can be divided into comprehensive corrosion and local corrosion. The former is also called uniform corrosion or overall corrosion, which refers to the uniform corrosion and loss of the material surface in contact with the environment. The corrosion of aluminum in alkaline solution is a typical uniform corrosion, such as alkali cleaning. The corrosion result is that the aluminum surface becomes thinner at approximately the same rate and the weight is reduced.
Localized corrosion means that the occurrence of corrosion is limited to specific areas or parts of the structure, and can be divided into the following categories:
Pitting corrosion occurs in very localized areas or parts of the metal surface, causing holes or pits that expand inward and even cause perforations. Aluminum in chloride-containing aqueous solutions is a typical pitting corrosion. In the corrosion of aluminum, pitting corrosion is common and is caused by the potential of a certain area of aluminum being different from the potential of the matrix, or by the presence of impurities with potentials that are different from the potential of the aluminum matrix.
This kind of corrosion is a selective corrosion that occurs at the grain boundaries of metals or alloys when the grains or crystals themselves are not significantly eroded. It will drastically reduce the mechanical properties of the material, causing structural damage or accidents.
The reason for intergranular corrosion is that the grain boundaries are very active under certain conditions. For example, there are impurities at the grain boundaries, or an alloy element increases or decreases at the grain boundaries. This means that there must be a thin region on the grain boundary that is electronegative to the rest of the aluminum, which corrodes preferentially. This kind of corrosion can occur in high-purity aluminum in hydrochloric acid and high-temperature water. AICu, AI-Mg-Si, Al-Mg, and Al-Zn-Mg alloys are all sensitive to intergranular corrosion.
Haomei Alumium provides rich marine aluminum alloys like 5083, 5052, 5086, 5059, 6061, 6082,etc. All are with classification society certification like DNV,LR, ABS,etc. Welcome to leave message below to inquire 5083 aluminium specification.
Original Source:https://www.marinealu.com/a/what-are-the-corrosion-resistance-of-aluminum-alloy-grades.html
Aluminium Foil for Medicine Packaging
Metal packaging material refers to a material that is rolled into thin sheets after special treatment and used for product packaging. It is also known as the "four major packaging materials" along with glass, plastic, and paper. It is one of the commonly used packaging materials for pharmaceuticals. Tin-plated iron sheets appeared in Czechoslovakia as early as 1200 AD; British tinplate technology was born in Britain in 1810; aluminum plates and aluminum foil for medicine packaging appeared in the early 20th century.
Metal packaging materials mainly include low carbon steel sheets, tinned steel sheets, non-tinned steel sheets, aluminum foil and aluminum alloy sheets. However, due to the particularity and strict requirements of pharmaceuticals, low carbon thin steel sheets and non-tinned steel sheets are used in food, beverage and industrial fields, but has few applications in the medical field. There are two main types of commonly used medicinal metal packaging materials:
1. Tin-plated steel plate: It is often used for packaging of sprays and aerosols;
2. Aluminum products( medicine aluminum foil and aluminum tubes): It is widely used in the packaging of tablets, capsules, granules, creams, ointments, gels and other solid or semi-solid preparations; aluminum products can also be combined with aluminum-plastic combination cover and the glass container.
Tablet bottles are used to package solid drugs such as tablets and capsules. These drugs are easily affected by moisture and may become ineffective or even deteriorate when exposed to water vapor. How to ensure the stability of the drugs within the validity period and avoid being affected by external moisture and deterioration? Its packaging can meet this demand very well.
Tablet bottles are generally made of plastic materials processed through various processes. First of all, these plastic products have good barrier functions against external water vapor, impurities, etc., and are good materials for pharmaceutical packaging, especially tablet drugs that are afraid of moisture.
Secondly, the caps of tablet bottles are generally sealed with pharma lidding foil. Aluminum foil is a hot stamping material that is directly rolled into thin sheets of metallic aluminum. Adding an aluminum foil sealing gasket between the body and cap of the medicine bottle can ensure the sealing of bottles.
The gasket of this sealing method is composed of adhesive sealing layer, aluminum foil, weak adhesive layer, cardboard elastomer, etc. The aluminum foil gasket is embedded in the bottle cap to expose the aluminum foil, and then applied to the bottle body to tighten the bottle mouth, using electromagnetic induction.
Medicinal sealing aluminum foil gaskets are mainly used inside various types of medical bottle caps. Its main function is to block direct contact between the bottle mouth and the inside of the bottle cap, thereby preventing contact between the inside of the bottle cap and the outside air. It can keep the quality of medicines unchanged for a long time. The aluminum foil 1100 is chosen.
Original site: https://www.alumhm.com/a/aluminium-foil-for-medicine-packaging.html
Aluminum Closure Sheet for Bottle Cap Cut to Size
With quality raw material and mature production technology, we can produce plain aluminum, painted and printed aluminum shee for making bott...
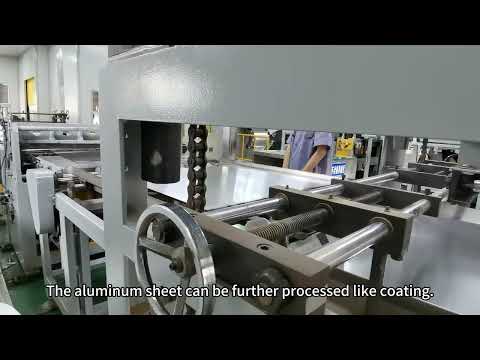
-
With the spread of energy saving and emission reduction concept, lightweight vehicles have been quickly promoted. Aluminum alloy is one of...
-
In the vast world of aluminum alloys, 5052 and 5754 aluminum alloys have become effective materials in many fields due to their unique pro...
-
In the field of food packaging, the packaging of butter is crucial. It not only ensures the quality and freshness of butter, but also attr...