In 1906, German Wilm accidentally discovered that after a certain period of time at room temperature, the strength of aluminum alloy would gradually increase with the prolonged storage time. This phenomenon was later referred to as age hardening, and as one of the earliest core technologies to promote the development of the aircraft aluminum sheets.
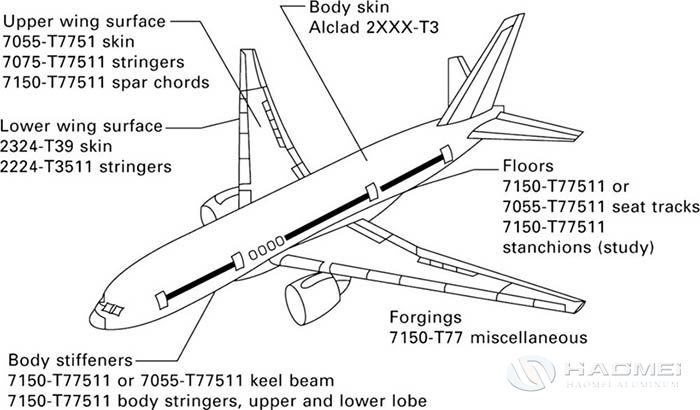
In the following hundred years, aircraft aluminum sheet manufacturers has made many research on aluminum alloy composition and synthesis methods, and the aluminum alloy processing technology such as rolling, extrusion, forging, heat treatment,etc.
The aircraft aluminum plate has the advantages of high strength, good processing and formability, low cost and good maintainability. It is widely used in aircraft main structure materials. The improvement of the aircraft properties such as flight speed and structural weight reduction put forwards higher requirements for the aluminum alloys.
There are four main kinds of aircraft aluminum alloys: 2024,7075,7050 and 6061 aluminum sheet. 2024 aluminium sheet has high fracture toughness and low fatigue crack growth rate. It is the most commonly used aircraft fuselage and underwing material.
7075 aluminum plate was successfully developed in 1943. It was successfully applied to the B-29 bomber. The strength of 7075-T6 aluminum alloy is the highest, but but its resistance to stress corrosion is poor.
7050 aluminum plate is developed on the basis of 7075 aluminum alloy, which has better strength, anti-flaking corrosion and stress corrosion resistance, and is applied to the compression components of F-18 aircraft.
6061 aluminum sheet can also be used on the aircraft. It has good corrosion resistance and excellent welding performance, but the strength is moderately low.
没有评论:
发表评论