The PTP packaging usually consists of two layers: one layer is PTP blister foil and the other layer is plastic film like PVC hard. They both need to satisfy the medical requirements.
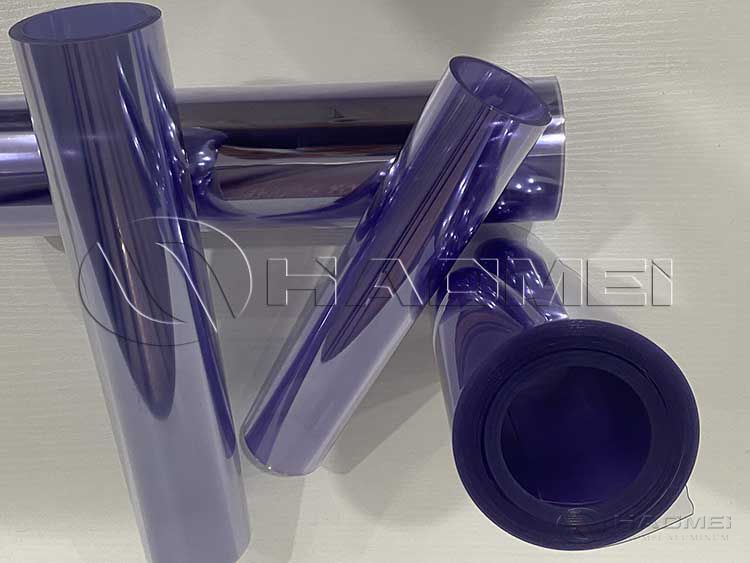
PTP aluminum foil testing items
1. Aluminum foil thickness: measure the straight-line distance from one side of the ptp aluminum foil to the other to determine its density and possible uses.
2. Aluminum foil width: evaluate the horizontal extension range of the aluminum foil to determine its covering or packaging capabilities.
3. Aluminum foil length: measure the maximum linear dimension of the aluminum foil along its main direction, used to calculate the total amount of material.
4. Aluminum foil surface quality: check the appearance and surface condition of the aluminum foil, including smoothness, scratches or other defects.
5. Aluminum foil tensile strength: measure the ability of aluminum foil to maintain structural integrity when subjected to tensile force.
6. Aluminum foil elongation: measure the degree to which aluminum foil can be stretched before breaking, reflecting the plasticity of the material.
7. Aluminum foil hardness: test the ability of aluminum foil to resist shape changes, such as indentation or scratches.
8. Aluminum foil thermal properties: analyze the physical behavior of aluminum foil at different temperatures, such as thermal expansion and contraction.
9. Aluminum foil conductivity: evaluate the conductivity of aluminum foil, which is key to electrical applications.
10. Corrosion resistance of aluminum foil: Test the resistance of aluminum foil to corrosive substances in the environment and predict its service life.
11. Abrasion resistance of aluminum foil: Measure the characteristics and durability of aluminum foil to maintain performance under physical friction.
12. Pressure resistance of aluminum foil: Analyze the ability of aluminum foil to withstand pressure without deformation or damage.
13. Fatigue resistance of aluminum foil: Evaluate the durability and fracture resistance of aluminum foil under repeated stress.
14. Anti-oxidation performance of aluminum foil: Determine the ability of aluminum foil to resist oxidation reactions such as rust and corrosion.
15. Thermal expansion coefficient of aluminum foil: Quantify the ratio of aluminum foil size change when temperature changes.
16. Thermal conductivity of aluminum foil: Test the efficiency of aluminum foil in transferring heat energy.
17. Thermal stability of aluminum foil: Evaluate the changes in aluminum foil performance under long-term exposure to high temperature.
18. Electromagnetic shielding effectiveness of aluminum foil: Measure the blocking effect of aluminum foil on electromagnetic wave interference.
19. Aluminum foil reflectivity: Determine the proportion of light or radiation energy reflected by the surface of the aluminum foil.
20. Aluminum foil air permeability: Evaluate the degree of aluminum foil's barrier to gas penetration.
21. Aluminum foil moisture permeability: Measure the aluminum foil's permeability to water vapor to determine its moisture-proof effect.
22. Aluminum foil hygroscopicity: Evaluate the ability of aluminum foil to absorb surrounding moisture, affecting storage and use.
23. Aluminum foil heat resistance: Test the stability of aluminum foil to maintain its original properties under high temperature environment.
24. Aluminum foil cold resistance: Test the ability of aluminum foil to resist embrittlement or breakage under extremely low temperature conditions.
25. Aluminum foil weather resistance: Determine the durability of aluminum foil exposed to the natural environment (sunlight, rain, etc.).
26. Aluminum foil chemical corrosion resistance: Analyze the aluminum foil's ability to protect against corrosion by various chemical substances.
27. Aluminum foil salt spray corrosion resistance: Test the effectiveness of aluminum foil's anti-corrosion in a salt spray environment.
28. Aluminum foil acid corrosion resistance: Measure the performance of aluminum foil against corrosion by acidic substances.
29. Spark resistance of aluminum foil: evaluates the degree to which aluminum foil is not flammable or produces sparks when in contact with a fire source.
30. UV resistance of aluminum foil: tests the ability of aluminum foil to resist aging or fading caused by ultraviolet radiation.
Polyvinyl chloride material itself is non-toxic, but polyethylene monomer has liver cancer-causing effects, so when using it, it is necessary to pay attention to the fact that the polyvinyl chloride monomer content of PVC sheets used for pharmaceutical packaging should be controlled within one part per million; on the other hand, polyvinyl chloride material has poor heat resistance and is easily deformed by heat. It is often necessary to add stabilizers and plasticizers to lower the processing temperature and adjust the hardness of PVC. Non-toxic additives should be selected for medicinal hard PVC sheets.
Original Source: https://www.alumfoils.com/a/ptp-packaging-ptp-blister-foil-and-hard-pvc.html