With 20 years'development, Haomei has grown into a top aluminium alloy manufacturers and suppliers. We have comprehensive kinds of aluminium sheets, aluminum coil, aluminum strip, aluminum foil, aluminum discs, aluminum tread plate, color coated aluminum and CTP plates, covering series-1, series-3,series-5, series-6 and series-8. You can realize one-stop purchase in Haomei.
Various Bottle Caps Made of Aluminum Foil Sheet
1235 Aluminum Foil for Lithium Battery
Aluminum foil battery acts as a positive current collector in lithium batteries due to its good properties. Battery aluminum foil has the characteristics of good conductivity, soft texture, cost advantage, stable performance at high potential.
The above characteristics are well adapted to the requirements of power batteries for current collectors. The power batteries currently used in new energy vehicles include ternary lithium batteries and lithium iron phosphate batteries, both of which are lithium-ion batteries.
Battery aluminum foil has a low weight and cost, and is relatively secretive among the components of lithium batteries. Battery aluminum foil accounts for 5% by weight, followed by positive electrode materials, negative electrode materials, electrolytes, and copper foil.
The cost accounts for about 3% of the total cost of lithium batteries, followed by lithium battery cathode materials, separators, negative electrode materials, copper foil, and electrolytes. The low weight and cost ratio often make people ignore its importance.
To further illustrate the importance of battery aluminum foil, we can compare it with other materials. In terms of chemical properties, the aluminum surface has a dense oxide layer and a high chemical potential, which can prevent the oxidation of the current collector and corrosion by the electrolyte, and at the same time, the lithium insertion reaction (LiAL alloying reaction) will not occur.
In terms of mechanical properties, it is easy to process, has good mechanical strength, can be welded and riveted, and has a soft texture, which can ensure that the pole piece does not break during winding, and has good thermal and electrical conductivity. In terms of cost, it has large reserves. The cost accounts for only 3% of the total cost of lithium batteries and is not a heavy metal or strategic metal resource.
Battery aluminum foil has higher purity. Currently, the battery aluminum foil produced in the market is mainly made of 1060, 1070, 1100 and 1235 aluminum foil. The above alloys all belong to the 1000 series. This series of alloys contains a large amount of aluminum, and the purity can reach more than 99.00%. Since it does not contain other technical elements, the production process is relatively simple and the price is relatively cheap. It is currently the most commonly used series in conventional industries.
Original source: https://www.hmaluminumsupply.com/a/1235-aluminum-foil-for-lithium-battery.html
Is The Aluminium Strip Easy to Scratch
Aluminium strip is a thin but strong metal strip made of aluminum alloy and is widely used in construction, electronics and packaging. However, the surface of aluminum strips is prone to scratching problems. So, why does aluminum strip scratch easily? How can we prevent this problem?
One of the reasons why the surface of aluminum strips is easily scratched is due to the relative softness of the aluminum alloy. Aluminum metal is less hard than other metals, such as steel. This makes the aluminum strip more susceptible to scratches by sharp objects on the surface. Accidental use of sharp objects, such as keys or pins, to rub against the surface of the aluminum strip can cause visible scratches.
On the other hand, the surface of the aluminum strips for sale is also susceptible to corrosion by chemicals. Some chemicals, such as acids, salts, alkali, etc., can cause oxidation reactions in aluminum strips. This reaction can lead to a harsh oxide layer on the surface, which affects the overall aesthetics of the aluminum strip. In addition, some strong acidic or alkaline solutions are more likely to cause deep corrosion, causing the aluminum strip to lose its original strength and durability.
How to effectively avoid scratches on the surface of aluminum strips? Firstly, we can apply a protective coating to the surface of the aluminum strip. This coating can increase the hardness of the aluminum strip to a certain extent, making it more resistant to scratches. In addition, this coating prevents chemical corrosion of the aluminum strip. In terms of coating selection, environmentally friendly coatings are recommended.
When we use aluminum strips daily, we should pay attention to avoid direct contact with sharp objects. For example, we can place the aluminum strip in a place free of sharp objects, or wrap it in a special protective cover to reduce the risk of scratches. In addition, care should be taken during handling and storage to avoid collision with hard surfaces or other sharp objects.
For scratched aluminum strips, we can try some repair methods. For example, minor scratches can be polished using a metal polish to eliminate or reduce the appearance of the scratch. For deeper scratches, consider using aluminum tape repair compound or decals to repair localized scratches. However, these methods are only suitable for small scratch repairs. Larger scratches may require a more complete repair or replacement. Welcome to leave message below to inquire aluminum ceiling strips price.
Original source: https://www.aluminumstrip24.com/news/is-the-aluminium-strip-easy-to-scratch.html
Aviation Aluminum Alloy 2024 7075
Aluminum alloys are one of the most widely used materials in aviation field. hey have good mechanical properties and process characteristics, and are characterized by high strength, light weight, and good toughness. They are one of the most important members of the civil aircraft structural material family.
The main features of Al alloy 2024 are large-scale and integrated, thin-walled and lightweight, precise cross-sectional dimensions and geometric tolerances, and uniform and high-quality structural properties. Aluminum alloys used in aerospace are mainly high-strength aluminum alloys, heat-resistant aluminum alloys, and corrosion-resistant aluminum alloys. High-strength aluminum alloys are mainly used in aircraft fuselage components, engine nacelles, seats, control systems, etc.
Al alloy 2024 is a typical hard aluminum alloy in the aluminum-copper-magnesium system. It contains 4.5% copper, 0.6% manganese and 1.5% magnesium. Its composition is reasonable and its overall performance is good. It is the most heavily used among the duraluminum alloys. 2024 aluminum alloy is commonly used in T3 and T4 tempers, which have high plasticity, fatigue life, fracture toughness and resistance to fatigue crack growth, but poor corrosion resistance.
2024 T3 aluminum not only has high strength, but also has excellent fatigue resistance. Welding is generally not recommended. Typical uses for 2024-T3 Alclad aluminum sheet are fuselage and wing skins, roofs, aircraft structures, and repair and restoration. Its ultimate strength is 62,000 PSI and shear strength is 40,000 PSI.
Aircraft manufacturers use high-strength alloys (mainly Alloy 7075) to strengthen aluminum aircraft structures. Aluminum alloy 7075 has copper (1.6%), magnesium (2.5%) and zinc (5.6%) for ultimate strength, but the copper content makes it very difficult to weld. 7075 aluminum has the best machining performance and can achieve very good results. The ultimate strength is 33000 PSI(-0) and 82000 PSI(-T6), and the shear strength is 22000 PSI(-0) and 49000 PSI(-T6).
7075 aluminum sheet’s common tempers are T6, T73, T76 and T74. 7075 t6 alloy has the highest strength, low fracture toughness, and is sensitive to stress corrosion cracking. It is generally not recommended for use in low temperature applications. The thermal conductivity of the material is related to its state. At 25℃, the thermal conductivity of the 7075-t6 is 124W/(m·℃), while that of the T73 material is higher, 156W/(m·℃). The specific heat capacity of 7075-T6 alloy (at 25℃) is 796J/(kg·℃).
Original source: https://www.aircraft-aluminium-sheet.com/a/aviation-aluminum-alloy-2024-7075.html
Aluminum Alloy 6101 5754 for High-speed Railway
High-speed rail carriages are welded with aluminum, and some high-speed rail lines pass through high-cold zones of minus 30 to 40 degrees Celsius; some instruments, equipment and daily necessities on Antarctic research ships are made of aluminum and need to withstand temperatures of minus 60 to 70 degrees Celsius. Can they function properly in such a cold environment? No problem, aluminum alloys are the latest afraid of cold and heat.
Aluminum alloys are the best low-temperature materials. They have no low-temperature brittleness. They are not as obvious as ordinary steel and nickel alloys. Although the steel’s strength properties increase as the temperature decreases, its plasticity and toughness decreases with the decrease of temperature, that is, it has obvious low-temperature brittleness. However, the aluminum alloys’ mechanical properties increase significantly with the decrease of temperature, regardless of the composition of the material, whether it is cast aluminum alloy, deformed aluminum alloy, powder metallurgy alloy, or composite material.
Aluminum alloys for high-speed rail carriages include Al-Mg series 5005 alloy sheets, 5052 alloy sheets, 5083 alloy sheets and profiles, Al-Mg-Si series 6061 alloy sheets and profiles, aluminum alloy 6101,6063 alloy profiles, Al-Zn-Mg series 7N01 alloy plates and profiles, and 7003 alloy profiles. The standard states are O, H14, H18, H112, T4, T5, and T6.
No matter what kind of aluminum alloy, its mechanical properties increase as the temperature decreases, so aluminum is an excellent low-temperature structural material, used for rocket cryogenic fuel (liquid hydrogen, liquid oxygen) storage tanks, liquefied natural gas (LNG) transportation ships and shore-based storage tanks, low-temperature chemical product containers, cold storage, refrigerated trucks, etc.
The aluminum plates used in the current manufacturing and maintenance of rail vehicle bodies include 5052, 5083, 6061, 5454 aluminum and the extruded profiles used include 5083, 6061, 7N01, etc. In addition, some new alloys such as 5059, 5383, 6082, etc., also has applications. It is best to use friction stir welding (FSW), which not only has high welding quality, but also does not require welding wire.
We can divide the aluminum alloys of the car bodies into according to the train operating speed: those used for vehicles with speeds <200km/h can be called first-generation alloys. They are conventional alloys and are mostly used to manufacture urban rail vehicle bodies, such as 6063, 6061 and 5083; second-generation aluminum alloys such as 6N01, 5005, 6005A, 7003, 7005 alloy, etc. are used to manufacture high-speed rail vehicle bodies with speeds of 200km/h~350km/h; third-generation alloys are 6082. Haomei Aluminum has all these aluminum alloys. Welcome to leave message to inquire what you need.
Original source: https://www.aluminium-auto-sheet.com/a/aluminum-alloy-6101-5754-for-high-speed-railway.html
Marine Grade Aluminum Diamond Plate and Marine Pipes
The aluminum tread plates are mostly made of 1060, 3003, 5052 and 6061. In comparison, the 1 and 3 series aluminum checker plates have lower hardness and slightly poorer wear resistance, and are mostly used in ordinary environments and applications where the anti-rust requirements are not strict.
The cabins of the shipbuilding industry all choose marine grade aluminum diamond plates, which have good anti-skid effect, strong anti-rust ability and light weight. 6061 patterned plate is a patterned aluminum plate with high hardness. The hardness is around 95HB in the T6 state. The bending performance is not good, but the hardness and strength are good.
5083 marine grade aluminum diamond plate has good corrosion resistance and anti-rust performance, and can adapt well to high-strength and high-corrosion resistance occasions. It has good application effects in ships, vehicles, and work platforms.
The 5086 marine aluminum tread plate after surface embossing is also the best material for spiral stairs, pedals, refrigerated truck sidings and floors on large ships. 5086 aluminum sheet has excellent corrosion resistance. At the same time, because of the various patterns embossed on the surface, such as 2 bars, 3 bars, 5 bars,etc., it plays a more critical anti-slip property.
6061 and 6082 are two alloys to make marine aluminum extrusions. They good formability, weldability, machinability, and medium strength,which can still maintain good operability after annealing. They are mainly used in mechanical structures, including bars, plates, pipes and profiles.
6061 marine aluminum pipe is an all-round player among the 6 series aluminum alloys. It has excellent corrosion resistance, weldability and machinability, as well as good tensile strength and fatigue strength.
6082 aluminum alloy has high mechanical strength and excellent corrosion resistance, and is particularly suitable for the manufacture of structural parts in the fields of shipbuilding, bridge engineering, and transportation vehicles. Its light weight and high strength make it an ideal choice to replace traditional steel materials.
Original source: https://www.marine-aluminium-plate.com/a/marine-grade-aluminum-diamond-plate-and-marine-pipes.html
Aluminum Plate and Aluminum Coil for Tankers
Compared with ordinary carbon steel and stainless steel tank trucks, aluminum alloy tank trucks can not only significantly reduce the weight of the vehicle, improve transportation efficiency, but also extend the service life of the tank. The aluminium coil for tankers are usually 5083, 5182, 5754, 5454,etc.
5083 aluminum alloy is with high strength, high toughness, corrosion resistance, easy processing, good thermal conductivity and fatigue resistance. It is a good choice for aluminum for tank car bodies. 5083 ultra-wide aluminum plate is widely used in the tanker body, because tank trucks are generally longer, with a length of 4-12.5 meters.
5454 aluminum alloy plate is an aluminum-magnesium alloy that is suitable for use under high temperature conditions and has good strength and corrosion resistance at high temperatures. When the temperature is higher than 135°C for long-term use, 5454 (0/H111) has better strength than 5083 aluminum-magnesium alloy.
At present, most tanker truck manufacturers mainly use 5083 aluminum plate for tanker head, tanker body and the use of 5182 plates can better reflect its corrosion resistance and welding performance, and under the same loading quality, the tank wall thickness can be thinner and the weight can be higher light.
The 50583 and 5182 aluminum coil required for tank bodies of oil tankers and other chemical transport vehicles has the characteristics of large size, medium strength, high quality surface and high formability. In particular, the toughness and strength of 5083-H321 aluminum alloy will increase at low temperatures, making it very suitable for use in liquefied natural gas (LNG) storage tanks on transport ships.
5754 aluminum sheet can be used to make tank truck bodies and bulkheads. The magnesium content of 5754 aluminum plate is higher than that of 5052, so the machinability is better. The silicon content of 5754 aluminum plate is also higher than that of 5052. The silicon content affects the forging function and corrosion resistance of aluminum alloy, so the 5754 aluminum plate has better forging properties and corrosion resistance.
Original source: https://www.aluminium-tanker-plate.com/a/aluminum-plate-and-aluminum-coil-for-tankers.html
5454 5083 Aluminum Plate for Tank Head
Aluminum alloy plates are gradually being used in large quantities in special vehicles due to their unique advantages of low density, corrosion resistance, energy saving and environmental protection. 5083, 5454 and 5182 are currently commonly used aluminum tanker plates, which can be used to load oil, gasoline, chemicals, cement and other dense materials.
As a common 5xxx aluminum alloy, 5454 aluminum plate is widely used in oil tanks, tank truck body, marine facility pipelines, automobile wheels, etc. 5454 alloy aluminum plate performs well in various types of vehicles such as passenger cars, vans and oil tankers.
5454 aluminum is an alloy commonly used in the manufacture of tank bodies, and its temper is O or H111. Another popular temper is 5454 h32 aluminum. The main alloying elements of this alloy are Mg and Mn, and it has good strength and corrosion resistance at high temperatures.
5083 aluminum alloy is an important aluminum alloy with good corrosion resistance, strength and weldability. It is widely used in the fields of ships, aerospace and automobiles. Its comprehensive performance makes it suitable for various special environments and requirements.
5083 aluminum alloy sheet is also very easy to process. It can be processed into various shapes and sizes of tank car body parts through stamping, welding and other processes to meet the needs of different application scenarios. The aluminum alloy tanker made of 5083 aluminum plate is more wear-resistant and durable.
5083 ultra-wide aluminum plate is the main alloy material for aluminum tank trucks. 5083 ultra-wide aluminum plate is widely used in tank truck because the tank trucks are generally long, with a length of 4-12.5 meters. The width of the plate and the ultra-thin thickness require more precise control, which puts extremely high demands on production.
The width of the 5083 aluminum alloy plate commonly used in the market is 2.2 meter and the thickness is 5mm, 6mm, 7mm, and 8mm. The 5083 aluminum plate produced by the six-high cold rolling mill introduced by Haomei Aluminum can reach a maximum width of 2600mm, with stable performance, which meets the tank truck manufacturing requirements.
Original Source:https://www.aluminumtankerplate.com/a/5454-5083-aluminum-plate-for-tank-head.html
A Highlight of Aluminum Embossing Sheets
The aluminium embossing sheets are made of aluminum plate through external mechanical processing. It is rolled on the basis of the aluminum flat plate with a roller press to form a convex pattern on the surface of the aluminum plate. The main alloys are 1060, 1100, 3003 and 5052.
Its two popular patterns are 5 bar aluminum tread plate and orange peel pattern aluminum sheet. Since the pattern on the surface of the aluminum plate is arranged in parallel according to five convex patterns, and each pattern is at an angle of 60-80 degrees with other patterns, this pattern has excellent anti-slip performance. Haomei Aluminum can provide 5 bar aluminum diamond sheet with a thickness of 0.8-8.0mm.
The surface of the orange peel pattern aluminum plate presents a pattern similar to that of orange peel. It can generally be used as a heat preservation insulation layer and is used in refrigerators, freezers, air conditioners, and packaging. We can provide it with a thickness of between 0.15-3mm.
Rolling is a common method for making patterned aluminum plates. The main principle is to press patterns on the surface of aluminum plates to form uneven patterns and lines. Rolling can be divided into two types: one is to roll on the aluminum plate through a mold, and the other is to roll the aluminum plate using a roller press.
The quality of embossed aluminum sheets is mainly reflected in the pattern formation rate, pattern height, and pattern height difference. The aluminum embossed sheet not only has a good surface, but also has relatively high requirements in pattern height, aluminum plate thickness, surface quality, external dimensions, and mechanical properties. Usually we need to inspect its quality according to the international standards or customer requirements.
The pattern height of aluminum checker plate an reach 1.0-2.0mm in China, and 0.8mm is the mainstream. In conventional applications, the pattern height of 0.8mm is sufficient for anti-slip use, and this height can also achieve good anti-slip effect in projects at home an broad. Welcome to buy embossed aluminum from us.
Original source: https://www.hm-alu.com/a/a-highlight-of-aluminum-embossing-sheets.html
Aluminium 6xxx: 6061 and 6063
Aluminium 6xxx is a type of aluminum alloy composed of elements such as aluminum, magnesium and silicon. It includes 6061, 6063, 6082,etc., which are often used in aerospace, shipbuilding, automobiles, construction, electronics and other fields. 6 series aluminum alloy has excellent mechanical properties, corrosion resistance and machinability, and is one of the most widely used aluminum alloys.
Although 6000 series aluminum alloys such as 6061 and 6063 have low strength, they have good ductility and are often used in aircraft body frames and frame structures, bolt components, and door and window frames.
6061 aircraft aluminum is a cold-treated aluminum forging product suitable for applications with high requirements for corrosion resistance and oxidation resistance. It has good workability, excellent interface characteristics, easy coating and good processability. It can be used in low-pressure weapons and aircraft joints.
6063 aluminum is a commonly used aluminum alloy with good corrosion resistance and can be used in various environmental conditions. 6063 aluminum alloy has several different tempers: 6063-T6, 6063-T651, 6063 T7351 and 6063-O. What are 6063 t6 mechanical properties?
It also has good machinability and can be formed by extrusion, stretching, forging and other processes to produce products of various shapes and sizes. n addition to corrosion resistance and machinability, 6063 aluminum alloy also has some other properties. For example, it has high strength and hardness, which can meet some structural requirements.
6063 aluminum has excellent thermoplasticity and can be extruded at high speed into thin-walled and hollow profiles with complex structures or forged into forgings with complex structures. It has a wide quenching temperature range and low quenching sensitivity. After demolding, it can be quenched by water spraying or water penetration as long as the temperature is higher than the quenching temperature. Thin-walled parts (6<3mm) can also be quenched by wind.
Hardness, a professional term in physics, refers to the ability of a material to locally resist the pressure of a hard object into its surface. The local resistance of a solid to the invasion of an external object is an indicator for comparing the softness and hardness of various materials. The Webster hardness of 6063 aluminum alloy should be around 12, and the Brinell hardness should be 120-160HB.
Haomei Aluminum has 2xxx, 5xxx, 6xxx and 7xxx aircraft aluminum alloys. Welcome to inquire al 6061 t6 price and other alloys you need.
Original Source:https://www.aircraftaluminium.com/a/aluminium-6xxx-6061-and-6063.html
Tres tipos de planchas offset
Después del pulido electrolítico y la oxidación anódica, se recubre la superficie de las planchas offset con una capa de material fotosensible. Incluye placa PS positiva, placa CTCP/UV-CTP y planchas ctp.
Placa PS positiva
Las planchas utilizadas en el proceso CTF son principalmente planchas de PS, es decir, planchas fotosensibles prerrevestidas, que se desarrollan para adaptarse al rápido desarrollo de la impresión litográfica. La placa de PS está compuesta por un sustrato de aluminio y un revestimiento de placa de PS.
La parte lipófila de la placa de PS es una resina diazo fotosensible con una altura de aproximadamente 3 μm en el plano base. Es una buena película lipófila e hidrófoba, y la tinta es fácil de esparcir sobre ella, pero el agua es difícil de esparcir.
Si se hornea a una temperatura de 230-240 °C durante 5-8 minutos, la película fotosensible se esmaltará y también mejorará la dureza de la plancha de impresión, y la durabilidad de la impresión de la plancha de impresión puede alcanzar los 200.000- 300.000 hojas.
La parte hidrófila de la placa de PS es una película delgada de óxido de aluminio con una altura de 0,2 a 1 μm. Su hidrofilicidad, resistencia a la abrasión y estabilidad química son relativamente buenas, por lo que la durabilidad de la impresión de la plancha de impresión también es relativamente alta.
Placa CTCP
La tecnología de impresión de planchas CTCP es una solución de fabricación de planchas por ordenador basada en las condiciones de impresión existentes. Aunque el precio de las planchas de impresión CTP ha bajado considerablemente después de años de producción en masa, todavía no puede bajar al nivel de precios de las planchas de PS, y las planchas utilizadas en la fabricación de planchas CTCP son planchas de impresión convencionales baratas, es decir, planchas de PS.
Más importante aún, gracias al uso de planchas de PS, las imprentas pueden mantener el estado anterior en términos de inventario de planchas, capacitación de operadores y kits de lavado sin reinversión, por lo que los costos de mantenimiento posteriores son bastante bajos.
Placa térmica CTP
El ámbito comercial de las empresas de impresión comercial y de embalaje que tienen altos requisitos en cuanto a la calidad del material impreso suele incluir álbumes boutique de alta gama y productos de embalaje exquisitos, por lo que les gusta elegir la tecnología térmica CTP con prioridad en la calidad.
La característica de la placa ctp es que la plancha de impresión se graba con un láser con una longitud de onda de 830 nm o 1064 nm, y el contorno del punto obtenido es más claro y la forma del punto es más fuerte.
El punto débil de las planchas CTP térmicas es su baja sensibilidad, entre decenas y cientos de milijulios por centímetro cuadrado. Para lograr una eficiencia de producción adecuada, a menudo se utiliza tecnología de grabación en paralelo con múltiples rayos láser y el costo de la fuente de luz es relativamente alto.
Haomei Aluminium tiene estos tres tipos de planchas de impresión de aluminio para satisfacer las múltiples necesidades de impresión comercial, impresión de envases e impresión de periódicos. Bienvenido a dejar un mensaje a continuación para preguntar qué necesita.
Fuente original: https://www.placadealuminio.es/a/tres-tipos-de-planchas-offset.html
5000 Series VS6000 Series Aluminium Alloy in Vehicle Field
For car enthusiasts, it is crucial to understand the performance and application areas of different types of aluminum alloys in automobile manufacturing. 5000 and 6000 aluminum alloys are the two common types of automotive aluminum sheets. They have obvious differences in composition, application fields, uses, physical properties and processing techniques.
Different metal components
The main alloy component of 5 series aluminum alloy is magnesium, with a magnesium content of 3-5%. The alloy components of 6 series aluminum alloy are magnesium and silicon, one of which enhances corrosion resistance and the other enhances mechanical properties.
The typical grades of 5xxx aluminum alloys are 5052 al, 5083, 5086, 5059, etc. They are widely used in ship hull, fuel tank, airplane skins,etc. The typical alloys of 6xxx aluminum alloys are 6016, 6014, 6061,etc. They are often used as the panel vehicle like the car door.
Different applications
6 series aluminum alloy is mainly used for support in the industrial and construction fields. Because 6 series aluminum alloy has good mechanical properties, it has wider applications in these fields.
5 series aluminum alloys are mainly used in the from of aluminum sheets such as 5052 aluminum sheet, while 6 series aluminum alloys are mainly used in the form of aluminum profiles. Since the 6 series aluminum alloy has good deformability and the characteristics of hot extrusion profiles and die casting, it can be used to manufacture automotive panels, pipes and profiles, etc. The 5 series aluminum alloy can also be used in profiles, such as 5050 aluminum alloy.
Different physical properties
5 series aluminum alloy is characterized by low density, high tensile strength and high elongation. The 6 series aluminum alloy is characterized by medium strength, good plasticity, excellent corrosion resistance, especially no stress corrosion cracking tendency. Therefore, 6 series aluminum alloy is an alloy with a wide range of applications and broad prospects.
Different processing processes
For automobile manufacturing, there are also obvious differences in the processing processes of 5 series and 6 series aluminum alloys. 5 series aluminum alloys cannot be heat treated, while 6 series aluminum alloys can be heat treated, so special attention needs to be paid to selecting the appropriate treatment process during the manufacturing process. Alu 6014 is a main car body panel.
In automobile manufacturing, choosing the right aluminum alloy can not only improve the performance of the car, but also reduce manufacturing costs and increase the service life of the car. Haomei Aluminum has rich kinds of 5xxx and 6xxx automotive aluminum alloys. Welcome to inquire what you need from us.
Original Source:https://www.autoaluminumsheet.com/a/5000-series-vs6000-series-aluminium-alloy-in-vehicle-field.html
What Is Capacitor Aluminum Foil
An aluminum electrolytic capacitor is a capacitor with a positive electrode and a negative electrode. The basic structure of an aluminum electrolytic capacitor is composed of a layer of anode aluminum foil, a layer of cathode aluminum foil, and a layer of liner paper soaked in electrolyte and a natural oxide film sandwiched between them. It is a capacitor made of winding, and the electrodes are soaked in electrolyte and then sealed with an aluminum shell and a plastic cover.
Anode foil refers to the aluminum foil used as the anode in electrolytic capacitors. The anode foil is not only etched but also anodized during the production process of the capacitor. The negative electrode foil refers to the aluminum foil used as the negative electrode in the electrolytic capacitor. The cathode in an aluminum electrolytic capacitor is essentially an electrolyte paste, and the negative electrode foil is the lead of the cathode.
The capacitor aluminum foil(plain aluminum foil) is made from high-purity aluminum ingots through special refining, rolling, cleaning and cutting processes, and then processed through an etching process to obtain corroded foil, which is then anodized to obtain the formed foil. The corrosion process causes corroded pits to form on the mill finish aluminum foil, increasing its surface area and thus giving the aluminum electrolytic capacitor its high capacitance.
The capacitor aluminum foil is one of the most technical parts of the aluminum electrolytic capacitor device industry chain.
The complete industrial chain of electrode foil is: refined aluminum (high-purity aluminum ingot)-electronic aluminum foil(plain aluminum) -corrosion foil-formed foil-aluminum electrolytic capacitor-electronic machine (such as high-definition TV, etc.). In the electrode foil industry chain, the corrosion foil used to produce the final foil product is the most technically difficult and the most profitable link.
The aluminum foil is the core component of aluminum electrolytic capacitors. Inside the capacitor, the aluminum foil serves as the positive electrode. It is usually made of high-purity metal aluminum sheet. Haomei Aluminum provides aluminium foil jumbo roll for further process like etching or forming.
The 1 series and 3 series aluminum foils produced by Henan Haomei can be used in the manufacture of electronic foils, such as 3003 aluminum foil and 1235-o aluminum foil. The foil rolling mill introduced by Haomei Aluminum was designed and installed by Zhuoshen Company. It adopts ANDRITZ plate rollers and full hydraulic control, and cooperates with high-precision pressure sensors and servo valves to achieve an excellent roll gap and ensure the safety of electronic foil quality.
What Are Alloys of Aluminium Cap for Bottle
There are different kinds of aluminum caps for bottle. Anodized aluminum bottle caps have a smooth surface, good hand feel, and a unique metallic luster. They have a beautiful appearance and a large design space, which can effectively improve the grade of wine packaging, thereby increasing product sales. Alumina bottle caps can be used in most mid-range wine bottle packaging applications.
The electroplated aluminum cap is another popular wine and bottle cap. It can effectively create a high-end feeling for the product in terms of appearance and texture, which is the effect pursued by the packaging of cosmetics and wine.
Aluminum-plastic cap is a common packaging material, mainly used to seal and protect the contents of the container. Medical aluminum cap can effectively protect the quality and composition stability of drugs during the shelf life.
It has good physical, chemical and microbiological stability, will not decompose, age or react chemically with drugs, will not absorb drugs or change the properties of drugs, and ensure the stability of drug quality.
Aluminum pilfer proof bottle caps are made of high-quality special aluminum alloy and are mainly used for packaging of alcoholic beverages (steamed or non-steamed) and medical and health products, and can meet special requirements such as high-temperature cooking and sterilization.
1060 aluminum plate is also used to make aluminum-plastic caps. It is often used in the food packaging industry, such as beverage cans, edible oil cans, etc. Its non-toxic, odorless and pollution-free characteristics make it an ideal choice in the field of food packaging.
Testing is one of the important means to ensure the reliability of aluminum sheet contact with food. The testing standards of 1060 aluminum sheet usually include indicators such as aluminum ion release, heavy metal content, and bacterial count. Only aluminum sheets that meet the testing standards can be used in food packaging materials, thereby ensuring the reliability of aluminum sheet contact with food.
3105 aluminum alloy is a typical deep-drawing material. The aluminum content is 98%, with good rust resistance, good conductivity, high plasticity in the annealed state, good plasticity in semi-cold hardening, low plasticity in cold hardening, good corrosion resistance and good weldability.
The aluminum bottle cap material price is composed of the price of aluminum ingots and processing fees, which varies with different aluminum sheet manufacturers and specifications. Each aluminum sheet manufacturer has different quotations due to differences in scale, input costs, production technology, and sales models. For products of different specifications, the prices are of course different due to different production complexities. Haomei Aluminum promises to offer you the best price with best quality.
Original source: https://www.alclosuresheet.com/a/what-are-alloys-of-aluminium-cap-for-bottle.html
Marine Large Aluminum Sheet and Pipe
The construction and working environment of ships require that the materials should have good corrosion resistance, weldability, plasticity, and certain tensile strength, yield strength, elongation, impact resistance and other properties. Aluminum sheet and marine aluminum pipe can meet these requirements, so the application prospects of marine aluminum alloys in boat building is very broad.
The use of aluminum alloy profiles in ship-type transportation vehicles can be counted from the 1790s, and it has a history of more than 100 years. In the 1860s, people used the characteristics of aluminum alloys to solve the problems of ship spalling corrosion, intergranular corrosion and stress corrosion, which was a major progress in the development of marine aluminum alloys.
In the 1970s, in order to reduce the weight of ships, people increased the development and application of aluminum alloy profiles. With the development of aluminum profiles, the decline in aluminum prices, some advanced manufacturing processes and methods, and the increasing attention paid to the lightweight of ships, the application of aluminum profiles in ships has developed faster.
6xxx aluminum profiles are alloys with aluminum and silicon as the main elements. They are formed by high-temperature extrusion to form a strengthening phase of Mgzsi phase. This is an aluminum alloy profile that can be strengthened by heat treatment, that is, the Mgzsi strengthening phase can be precipitated by solid solution aging. This method can improve its strength, making it have high corrosion resistance, medium strength and good welding performance. The common 6xxx marine aluminum pipes are 6061 and 6082.
The aluminum plate for boat building is usually large aluminum sheet, of which the width is 2000 mm and 6000/8000/9000/12000mm in length. Thicknesses include 2mm, 3mm, 4mm, 5mm, 6mm, 8mm, 10mm, etc.
5083 aluminum sheet, 5xxx Al-Mg alloy, has high strength, corrosion resistance and weldability. It is currently widely used in ships and yachts, with medium and thick aluminum plates being the most commonly used, and the common tempers are H111, H112, H116, and H321.
Marine aluminum plates are immersed in water all year round and have high requirements for corrosion resistance. 5052 aluminum plates are Al-Mg alloys with excellent corrosion resistance and medium strength, which are suitable for the manufacture of economical aluminum alloy ships. In addition to being used in ship hull, 5052 aluminum plates can also be used in cable bridges, ship water tanks, cabin floors and other parts on ships.
Original Source:https://www.marinealu.com/a/marine-large-aluminum-sheet-and-pipe.html
How Will the Aluminum Sheet Thickness Affect Its Properties
The aluminum sheet thickness standard refers to the thickness range of the aluminum plate determined according to certain specifications during the production and application of the aluminum plate. Aluminum plates are widely used in construction, automobile manufacturing, electronics, aerospace and other fields. Therefore, determining the aluminum plate thickness standard is of great significance for ensuring product quality, promoting technological innovation and improving industry development.
The thickness of aluminum plate has a great influence on physical properties, including strength, toughness, and compressive resistance. Generally speaking, the thicker the aluminum alloy, the better the physical properties. However, if the thickness is too large, it will affect the processing performance of the aluminum plate.
Common measurement methods include hand measurement, caliper measurement, optical measurement, etc. Among them, optical measurement is a high-precision measurement method that can meet the measurement needs of high-precision aluminum sheets.
On the one hand, the thickness standard of aluminum plate is directly related to the stability of product quality and function. Qualified aluminum plate thickness can ensure that the mechanical properties, corrosion resistance and processing performance of the product meet the design requirements, and ensure the stability and reliability of the product during use. On the other hand, the formulation of aluminum plate thickness standards is also an important driving force for the continuous innovation and development of the aluminum industry. Accurate thickness standards help aluminum sheet manufacturers improve product quality, reduce costs, and promote technological progress.
The commonly used aluminum sheet thicknesses are 0.1mm, 0.2mm, 0.3mm, 0.4mm, 0.5mm, 0.7mm, 0.8mm, etc. Normal pipe insulation aluminum sheet can not be too thick. Aluminum sheet 0.5mm is a common choice, the width is 1 meter. Small rolls are commonly used, each roll is about 50 meters, and two people can lift it for easy operation.
The popular alloys are 1050, 1060, 3003, 3a21,etc. Among them, 1060 pure aluminum sheet or coil is basically chosen by 80% of the projects, and 3003 aluminum sheet, as an aluminum-manganese alloy, is mostly used in projects with high anti-corrosion requirements and relatively large corrosive environments, such as chemical plant desulfurization and insulation projects. You can choose according to your own project situation.
The polykraft laminted aluminum coil is also a product that has just emerged in recent years. Generally, it is used more by foreign users, especially in the Middle East. The thickness is generally 0.2-2.0mm and the width is between 800-1300mm. The alloy generally uses 3003, 3004 and 5052.
The biggest benefit of aluminum PCB sheet is its excellent heat dissipation capability, which transfers heat through the aluminum layer and quickly cools the components, thereby improving the overall performance of the final product. The thermal conductivity of PCB aluminum sheet s mainly achieved through the aluminum layer. Although there are many thicknesses to choose from, the most commonly used thickness is the aluminium sheet 1mm.
Original source: https://www.alumhm.com/a/how-will-the-aluminum-sheet-thickness-affect-its-properties.html
Aluminum Closure Sheet for Bottle Cap Cut to Size
With quality raw material and mature production technology, we can produce plain aluminum, painted and printed aluminum shee for making bott...
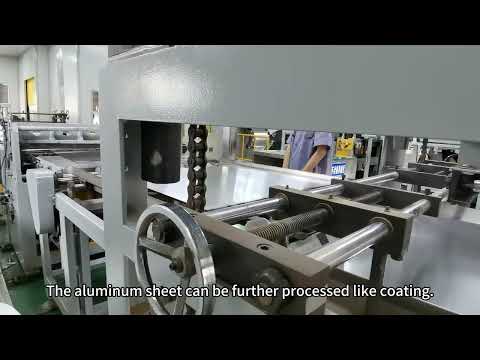
-
With the spread of energy saving and emission reduction concept, lightweight vehicles have been quickly promoted. Aluminum alloy is one of...
-
In the vast world of aluminum alloys, 5052 and 5754 aluminum alloys have become effective materials in many fields due to their unique pro...
-
In the field of food packaging, the packaging of butter is crucial. It not only ensures the quality and freshness of butter, but also attr...